Mastering Logistics: Quality Control Strategies for 3PL
In the competitive world of third-party logistics (3PL), quality control (QC) is a critical factor that can make or break a business. Ensuring that products are handled, stored, and shipped with the highest standards of care is essential to maintaining customer satisfaction and operational efficiency. In this comprehensive guide, we’ll explore the importance of QC in 3PL, the role of standard QC rules, Service Level Agreements (SLAs), and the necessity of matching items to packing lists.
The Importance of Quality Control in 3PL
Quality control in 3PL is not just about meeting customer expectations; it’s about exceeding them. It involves a series of processes designed to ensure that all aspects of logistics operations are performed to the highest standards. From warehousing to shipping, every step must be meticulously monitored to prevent errors, reduce waste, and improve efficiency.
Key Benefits of Quality Control:
- Enhanced Customer Satisfaction: Consistently delivering high-quality products ensures that customers are happy and loyal.
- Operational Efficiency: Streamlined processes reduce the risk of errors, leading to cost savings and faster turnaround times.
- Reputation Management: A strong QC system helps build a reputation for reliability and excellence.
- Compliance: Adhering to industry standards and regulations protects the business from legal issues.
Standard QC Rules: The Backbone of Quality Assurance
Standard QC rules are the foundation of any effective quality control system. These rules provide a consistent framework for evaluating and maintaining the quality of products and services. They include guidelines for inspecting products, handling materials, and documenting processes.
Key Elements of Standard QC Rules
- Inspection Procedures: Detailed guidelines on how to inspect products for defects and discrepancies.
- Handling Protocols: Instructions for safe and efficient handling of materials to prevent damage.
- Documentation: Comprehensive record-keeping to track inspections, findings, and corrective actions.
- Training: Ongoing training programs to ensure that all staff are knowledgeable about QC procedures.
Service Level Agreements (SLAs): Setting the Benchmark
Service Level Agreements (SLAs) are formal contracts between 3PL providers and their clients that define the expected level of service. SLAs are crucial for setting clear expectations and ensuring accountability.
Key Components of SLAs
- Performance Metrics: Specific criteria that measure the quality and efficiency of services provided.
- Response Times: Agreed-upon time frames for responding to and resolving issues.
- Penalties: Consequences for failing to meet the agreed-upon standards.
- Review Mechanisms: Regular evaluations to assess performance and identify areas for improvement.
Matching Items to Packing Lists: Ensuring Accuracy and Accountability
Matching items to packing lists is a critical aspect of QC in logistics. This process ensures that the correct items are shipped to the right destinations, reducing the risk of errors and customer dissatisfaction.
Steps for Effective Matching
- Verification: Cross-checking items against the packing list to ensure accuracy.
- Labeling: Properly labeling items to match the descriptions on the packing list.
- Documentation: Keeping detailed records of matched items for accountability.
- Auditing: Regular audits to identify and rectify discrepancies.
Common Challenges in QC and How to Overcome Them
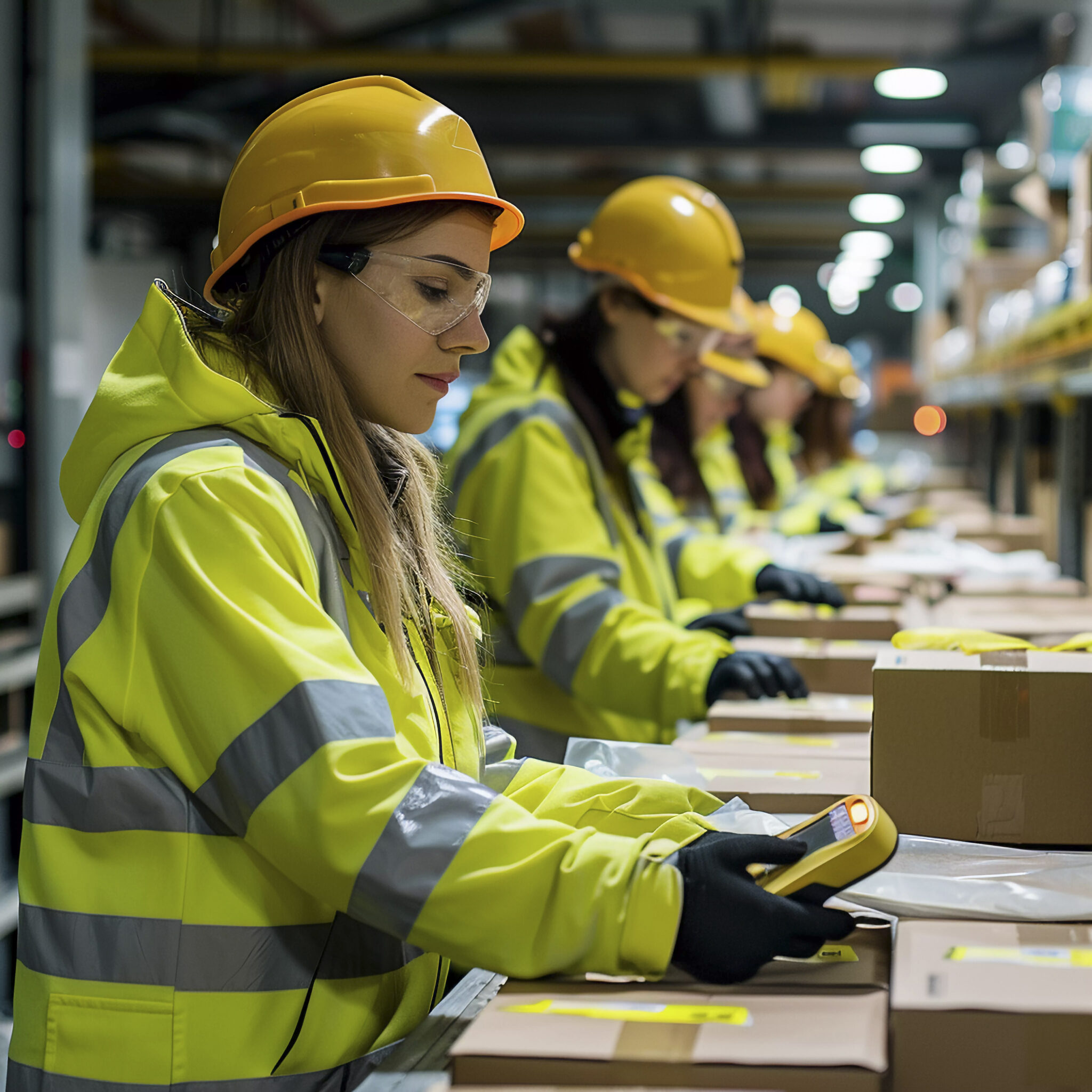
Quality control challenges are unavoidable, despite the best efforts. Here are some common challenges as well as ways to overcome them:
Challenge 1: Human Error
Human error is a significant challenge in logistics. To minimize errors, implement automated systems and provide regular training to your team. Encourage a culture of accountability and continuous improvement.
Challenge 2: Inconsistent Processes
Inconsistent processes can lead to quality issues. Standardize your QC procedures and ensure that all team members follow them consistently. Use checklists and automated tools to enforce standardization.
Challenge 3: Lack of Visibility
A lack of visibility into operations can hinder your QC efforts. Implement technology solutions that provide real-time data and insights into your processes. Use this information to make informed decisions and address issues promptly.
Challenge 4: Changing Client Expectations
Client expectations can change over time, making it challenging to maintain consistent QC standards. Regularly review and update your SLAs to align with your client’s evolving needs. Communicate openly with your clients to understand their expectations and address any concerns.
In the world of third-party logistics, quality control is paramount. Implementing robust QC strategies, adhering to standard QC rules, and establishing clear SLAs are essential for maintaining high standards of service. By focusing on matching items to packing lists, leveraging technology, and fostering a quality-first culture, 3PL providers can ensure customer satisfaction and operational efficiency. Remember, the key to mastering logistics lies in a commitment to continuous improvement and a relentless pursuit of excellence.